کایزن (Kaizen) یک فلسفه مدیریتی ژاپنی است که بر بهبود مستمر و تدریجی فرآیندها تأکید دارد. این روش در ابتدا در صنعت خودروسازی ژاپن بهویژه در شرکت تویوتا مطرح شد و امروزه در سازمانهای مختلف و حتی در زندگی شخصی کاربرد دارد.
فهرست مطالب
۱. مفهوم و ریشهی کایزن
ریشهی واژهی کایزن:
- Kai (改): تغییر یا اصلاح
- Zen (善): بهتر یا بهبود
بنابراین، کایزن به معنی “بهبود مداوم” است.
هدف اصلی کایزن:
- افزایش بهرهوری
- کاهش اتلاف
- بهبود مستمر کیفیت
کایزن در سازمانها:
- تمرکز بر پیشرفتهای کوچک اما مستمر
- ایجاد فرهنگ مشارکتی بین کارکنان
۲. اصول کلیدی کایزن
۱. بهبود مستمر:
- تغییرات کوچک اما مداوم
- نتایج پایدار در طول زمان
۲. مشارکت تمامی کارکنان:
- تمامی سطوح سازمان در بهبود فرآیندها سهیم هستند.
۳. حذف اتلافها (Muda):
- کاهش زمانهای غیرضروری
- جلوگیری از حرکتهای اضافی و خطاها
۴. استانداردسازی فرآیندها:
- جلوگیری از بازگشت به روشهای ناکارآمد
۵. تصمیمگیری بر اساس دادهها:
- استفاده از شواهد واقعی بهجای حدس و گمان
۳. مزایای اجرای کایزن
- افزایش بهرهوری از طریق کاهش اتلافها
- بهبود کیفیت و کاهش خطاها
- کاهش هزینهها از طریق بهینهسازی منابع
- افزایش رضایت کارکنان از طریق مشارکت در فرآیندهای بهبود
۴. تکنیکهای کاربردی در کایزن
1. چرخه (PDCA) دمینگ:
یک روش مشهور برای بهبود مستمر که شامل چهار مرحله است:
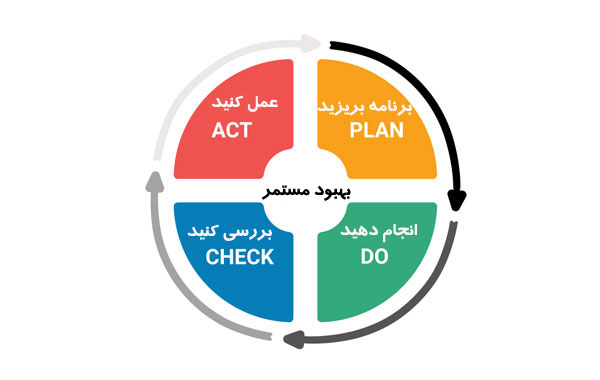
P (Plan) → برنامهریزی: شناسایی مشکل و طراحی راهحل
D (Do) → اجرا: پیادهسازی تغییرات در مقیاس کوچک
C (Check) → بررسی: تحلیل نتایج و بررسی اثربخشی
A (Act) → اقدام: استانداردسازی و گسترش تغییرات موفق
2. نظم و انظباط در محیط کار(5s):
یک روش ژاپنی برای بهینهسازی محیط کاری که شامل ۵ مرحله است:
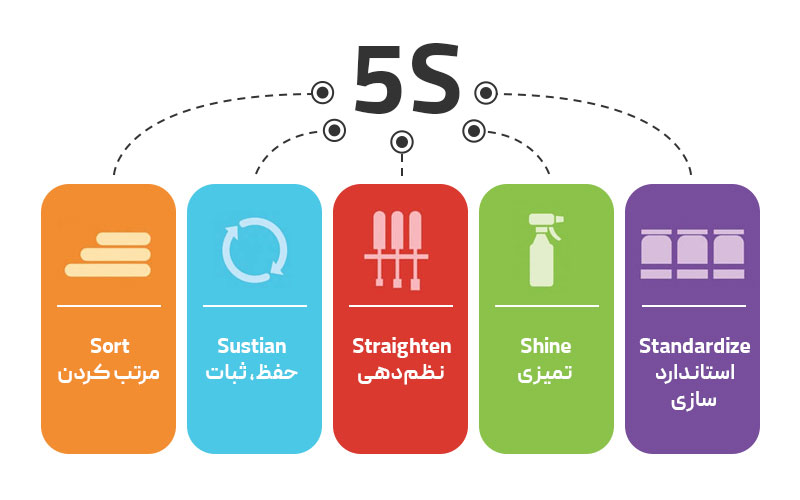
Seiri (جدا کردن): حذف اقلام غیرضروری
Seiton (مرتبسازی): سازماندهی ابزارها
Seiso (پاکیزگی): تمیز نگهداشتن محیط
Seiketsu (استانداردسازی): ایجاد قوانین برای حفظ نظم
Shitsuke (نظم و انضباط): عادت دادن کارکنان به رعایت این اصول
۳. کایزن بلیتز (Kaizen Blitz):
- اجرای سریع و فشرده تغییرات در چند روز
۴. تحلیل علت و معلول (Fishbone Diagram):
- یافتن دلایل اصلی مشکلات
۵. مقایسهی کایزن با نوآوریهای بزرگ
ویژگی | کایزن (بهبود مستمر) | نوآوری بزرگ (Innovation) |
نوع تغییر | تدریجی و مداوم | ناگهانی و بزرگ |
ریسک | کم | زیاد |
هزینه | پایین | بالا |
زمان اجرا | کوتاهمدت و پیوسته | بلندمدت و مقطعی |
تأثیر | پایدار و تدریجی | سریع اما ناپایدار |
۶. اجرای کایزن در زندگی شخصی
- مطالعهی روزانه حتی ۱۰ دقیقه بهجای انتظار برای فرصتهای بلندمدت
- ورزش کوتاه ۵ دقیقهای بهجای ترک کامل آن
- کاهش تدریجی هزینهها و مدیریت مالی هوشمندانه
- بهبود مهارتهای کاری با یادگیری مداوم
بهبود مستمر و کتاب تولید ناب (Lean Manufacturing)
بهبود مستمر (Continuous Improvement) یک اصل بنیادین در مدیریت و بهرهوری است که بر اصلاح مداوم و تدریجی فرآیندها تأکید دارد. این مفهوم، پایهی اصلی کایزن و تفکر تولید ناب (Lean Manufacturing) محسوب میشود. تولید ناب که ریشه در سیستم تولید تویوتا (TPS) دارد، به دنبال حذف اتلافها، افزایش بهرهوری و ارائهی ارزش بیشتر به مشتریان است.
یکی از مهمترین کتابهایی که این مفهوم را به طور کامل بررسی کرده است، کتاب “تولید ناب: ماشینهایی که جهان را تغییر دادند” نوشتهی جیمز ووماک، دنیل جونز و دانیل روس است. این کتاب به بررسی تحولاتی که در صنعت خودروسازی ژاپن به ویژه در شرکت تویوتا رخ داده، پرداخته و اصول تولید ناب را توضیح میدهد.
۱. مفهوم بهبود مستمر (Continuous Improvement)
بهبود مستمر به معنی بهینهسازی تدریجی فرآیندها و حذف ناکارآمدیها است. برخلاف تغییرات بزرگ و ناگهانی، این روش روی پیشرفتهای کوچک و پایدار تمرکز دارد.
اصول اصلی بهبود مستمر:
- تمرکز بر بهبود روزانه: تغییرات کوچک اما دائمی
- مشارکت کارکنان در همه سطوح: هر فرد در سازمان مسئول بهبود است
- حل مشکلات ریشهای: تحلیل و حذف عوامل ایجادکنندهی مشکلات
- استانداردسازی فرآیندهای بهینهشده: جلوگیری از بازگشت به روشهای ناکارآمد
- استفاده از دادهها برای تصمیمگیری: تصمیمگیریهای مبتنی بر شواهد
فواید بهبود مستمر:
- کاهش اتلافها و افزایش کارایی
- ارتقای کیفیت محصولات و خدمات
- کاهش هزینههای تولید و عملیاتی
- افزایش رضایت کارکنان و مشتریان
مثال در صنعت:
- تویوتا: از روشهای بهبود مستمر برای افزایش بهرهوری و کاهش هزینهها استفاده میکند.
- آمازون: با تحلیل دادهها و بهینهسازی فرآیندهای انبارداری و ارسال، بهبود مستمر را اجرا کرده است.
۲. تولید ناب (Lean Manufacturing) و کتاب “تولید ناب“
تعریف تولید ناب:
تولید ناب (Lean Manufacturing) یک سیستم مدیریتی است که بر حذف اتلافها (Muda)، افزایش کارایی و تولید محصولات با کیفیت بالا تأکید دارد. این مفهوم ابتدا در سیستم تولید تویوتا (TPS – Toyota Production System) توسعه یافت و سپس در سراسر جهان مورد استفاده قرار گرفت.
مهمترین نکات کتاب:
- تولید انبوه در مقابل تولید ناب:
- تولید انبوه (Mass Production) به حداکثرسازی تولید بدون توجه به نیاز واقعی بازار تمرکز دارد.
- تولید ناب به تولید بر اساس تقاضا و کاهش ضایعات تأکید دارد.
- پنج اصل تولید ناب:
۱. تعیین ارزش (Value): شناسایی آنچه که مشتری واقعاً نیاز دارد.
۲. جریان ارزش (Value Stream): تحلیل و حذف فعالیتهای غیرضروری در فرآیند تولید.
۳. ایجاد جریان پیوسته (Flow): بهینهسازی فرآیندها برای کاهش تأخیر و افزایش سرعت.
۴. تولید کششی (Pull): تولید فقط در صورت نیاز مشتری.
۵. بهبود مستمر (Kaizen): پیگیری و اصلاح فرآیندها به صورت مداوم. - حذف انواع اتلافها (Muda):
در تولید ناب، هفت نوع اتلاف اصلی شناسایی شده است که باید حذف شوند:
- تولید بیش از حد (Overproduction)
- انتظار (Waiting)
- حملونقل غیرضروری (Transportation)
- فرآیندهای غیرضروری (Overprocessing)
- موجودی اضافی (Inventory)
- حرکتهای غیرضروری (Motion)
- نقص و دوبارهکاری (Defects)
مزایای تولید ناب:
- افزایش بهرهوری و کارایی
- کاهش هزینههای تولید
- افزایش رضایت مشتریان
- کاهش زمان تحویل محصولات
- بیشتر بخوانید:
- پلتفرم پایش – نخستین پلتفرم رهگیری پرتفوی صندوق های سرمایه گذاری
- پیکوچارت | ابزار تحلیل تکنیکال
- سامانه رابین تریدر از کارگزاری هوشمند رابین
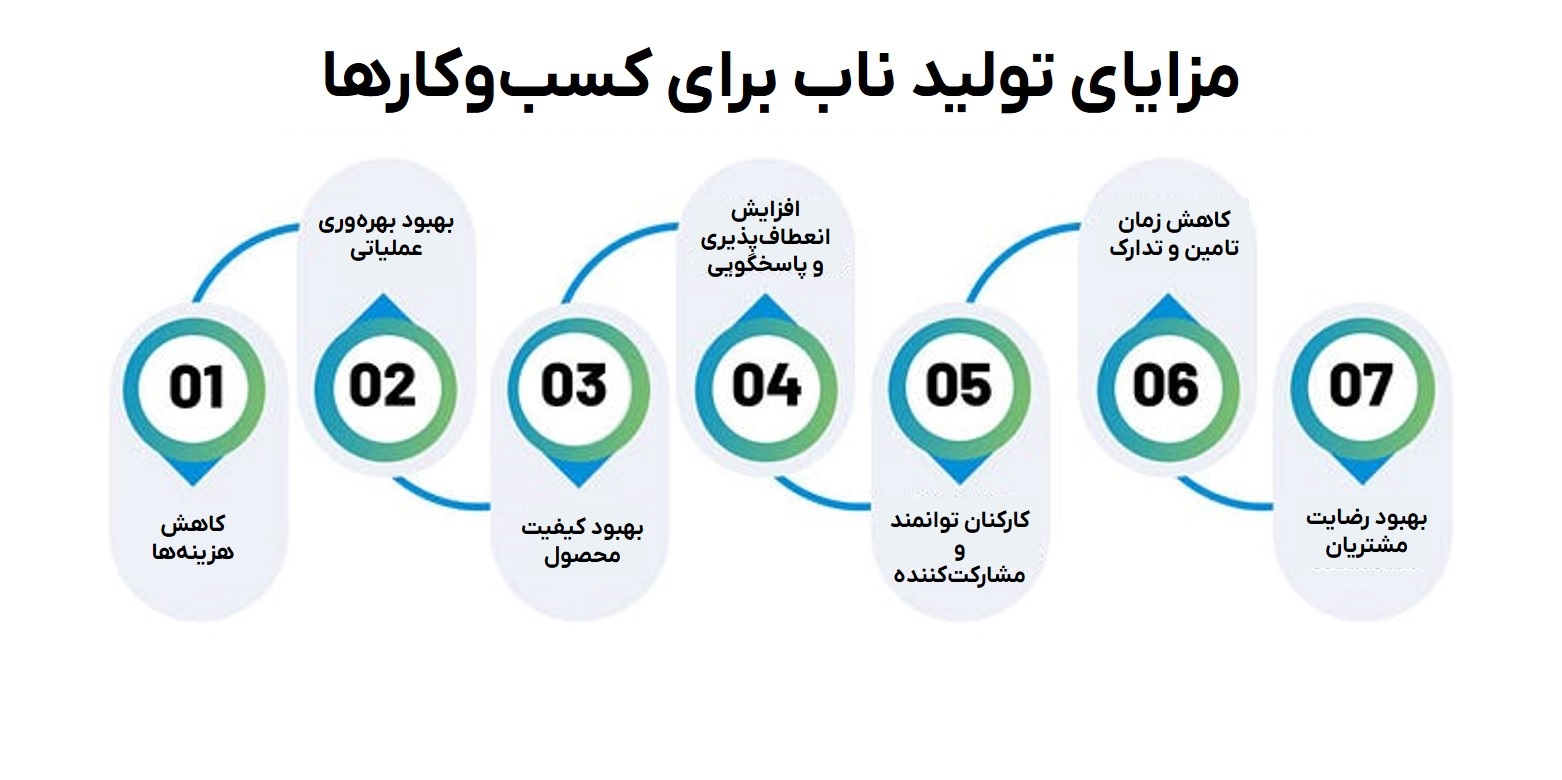
مثالهای موفق از تولید ناب:
- تویوتا: پیشگام در تولید ناب با استفاده از سیستم کانبان و مدیریت کیفیت.
- اپل: بهینهسازی زنجیره تأمین با کاهش موجودی اضافی و تولید بر اساس تقاضا.
- زیمنس: استفاده از Lean Manufacturing در خطوط تولید صنعتی.
۳. مقایسهی تولید ناب و بهبود مستمر
ویژگی | بهبود مستمر (Kaizen) | تولید ناب (Lean Manufacturing) |
هدف | افزایش تدریجی کارایی | حذف اتلافها و بهینهسازی تولید |
تمرکز | پیشرفتهای کوچک اما مداوم | تولید کارآمد و سریع |
استراتژی | اصلاح و بهبود فرآیندها | بهینهسازی کل سیستم تولیدی |
مقیاس اجرا | در هر بخش سازمان | در کل سازمان |
مثال | افزایش بهرهوری کارکنان، کاهش زمان انتظار | کاهش موجودی، بهینهسازی خط تولید |
۴. اجرای بهبود مستمر و تولید ناب در کسبوکارها
گامهای اجرایی:
- شناسایی مشکلات و اتلافها
- طراحی راهحلهای بهبود تدریجی
- اجرای چرخه (PDCA) برنامهریزی، اجرا، بررسی، اصلاح
- استانداردسازی فرآیندهای موفق
- مشارکت تمامی کارکنان در فرآیندهای بهبود
ابزارهای مورد استفاده:
- 5s : مرتبسازی، نظمدهی، پاکیزگی، استانداردسازی، انضباط
- کانبان : (Kanban) سیستم مدیریت جریان تولید و کاهش اتلاف
- شش سیگما : (Six Sigma)بهبود کیفیت و کاهش نقصها
سخن پایانی: قدرت بهبود مستمر و تولید ناب
بهبود مستمر (Kaizen) و تولید ناب (Lean Manufacturing) ، دو رویکرد قدرتمند برای افزایش بهرهوری، کاهش اتلافها و بهبود کیفیت هستند. این مفاهیم، نهتنها در صنعت، بلکه در هر سازمان و حتی زندگی شخصی نیز قابل اجرا هستند.
کایزن، بر تغییرات تدریجی و مستمر تأکید دارد، در حالی که تولید ناب به حذف اتلافها و ایجاد جریان کارآمد در فرآیندها میپردازد. ترکیب این دو روش، منجر به کاهش هزینهها، افزایش کارایی، بهینهسازی منابع و رضایت بیشتر مشتریان و کارکنان خواهد شد.
شرکتهایی مانند تویوتا، آمازون و اپل با استفاده از این اصول، به موفقیتهای بزرگ دست یافتهاند. راز موفقیت در بهبود مستمر، تعهد به تغییرات کوچک اما پایدار است.
“هر روز، یک قدم به جلو؛ کوچک اما مؤثر!”